6028 ZZ 140x210x33 Rulman
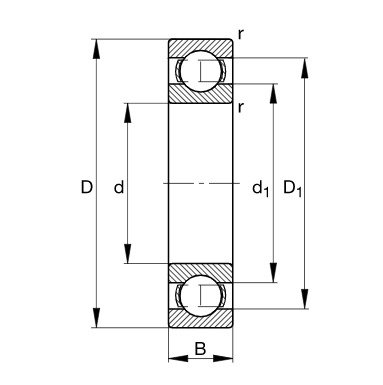
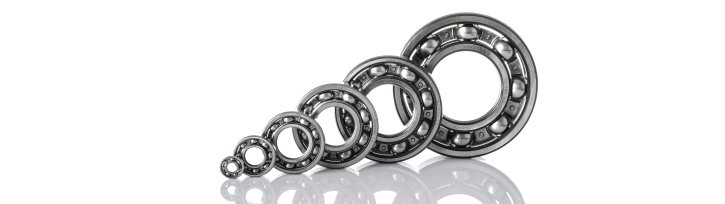
WHAT IS BEARING?
The main task of the bearing is to minimize the friction between the two elements with relative rotational motion and to provide trouble-free load transfer. Bearing is an element of every rotating mechanism. A perfect bearing creates a perfect mechanism. In reducer, ventilator and pumps, machine tool shafts, automobile shaft, axle, gearbox, belt tension system, alternator and steering systems, water pumps and doors, all kinds of industrial electric motors, washing machines and vacuum cleaners, agricultural machinery, heavy construction machinery Bearings are used in wind turbines, in short, in any rotating mechanism.
Bearing Components
cages
Cages are used to keep the rolling elements at equal distance from the periphery and to prevent them from rubbing against each other during rotation. Cages do not play a role in force transmission. Cages are grouped in the following ways according to their materials.
Sheet steel cage (J): Standard cage material is DC04-DC01-DC03. They can be used up to 150°C. Sheet metal cages are in 2 parts and these 2 half cages are attached to each other with rivets.
Plastic cage (TN) without glass wool reinforcement: They can be used up to 115°C. The general name of the material is P6.6. The technical definition of the nomenclature referred to as TN in ORS is A4H.
Glass wool reinforced Plastic cage (TN1): They can be used up to 150°C. The general name of the material is P6.6. The technical definition of the nomenclature referred to as TN1 in ORS is A3HG5.
Glass wool reinforced Plastic cage (TH1): They can be used up to 170°C. The general name of the material is P4.6. The technical definition of the nomenclature referred to as TH1 in ORS is Stanyl.
Solid brass cage (M): It is used in environments with heavy loads and vibrations. It is difficult and expensive to manufacture.
Steel or brass cages can be produced by pressing the appropriate material from sheet metal, massive cages by processing from brass material or by injection from plastic material. Recently, plastic cages with materials such as Polyamide 6.6, Polyamide 4.6 and normal or glass wool reinforced are preferred in many applications due to their light weight, slip, shock absorbing properties and cause less noise at high speeds. In addition, cages made of phenolic (phenolic) material can be used in line with customer request or application area.
caps
The covers prevent the grease inside the bearing from escaping and foreign matter from entering the bearing from the outside.
Sheet metal cover (Z): They are made of sheet metal, the material is TS 275 - DIN EN 10202. They can be used at higher speeds than rubber caps, as they do not rub against the inner ring.
Rubber cap (RS): They consist of various elastomer and steel sheet parts such as NBR, ACM, FKM, NDNN, HNBR. Since they work by rubbing against the inner ring, their sealing from the inside to the outside or from the outside to the inside is much better than sheet metal covers, but they are not suitable for high speed operation due to friction. But for high speeds, a less contact or non-contact design can be made that is relatively more suitable. Inner lip shapes are different according to various applications. (RSR, RS1, RDD etc.)
The operating temperatures for rubber-based materials to be considered are given below:
NBR : -30°C / +105°C (Max. 120 °C in short-term work)
NDNN : -40°C / +130°C (Max can reach 150°C in short-term work)
HNBR : -40°C / +150°C (Max can reach 170°C in short-term work)
ACM : -20°C / +150°C (Max can reach 170°C in short-term work)
FKM : -30°C / +200°C (Max can reach 230°C in short-term work)
Raceway Elements
They provide force transmission, play a role as the main factor in the classification of bearings.
The balls are spherical in shape, the friction forces in the bearings they are used are lower than the other bearings and they are preferred in rolling bearings rotating at very high speeds. In addition to steel balls, ceramic balls are used in bearings. The contact of the balls in the bearing is punctual.
The rollers used in the bearings are available in conical, cylindrical, spherical and needle roller types. They carry loads with linear contact in the bearing. In order to minimize the load distribution at the contact ends, their surfaces are curved. Since they have linear contact, they carry more load than ball bearings of the same size.
Lubrication Types and Grease
For reliable operation of bearings, they must be properly lubricated to prevent direct metal contact between the rolling elements and the raceways and to prevent surface wear. For this reason, the selection of the appropriate oil, lubrication method, etc. elements are important.
Greases, oils, and in some special cases, solid oils can be used to lubricate bearings. Lubrication reduces friction, hence wear, and prevents rusting. Oil can also take on the role of cooling and sealing. The formation of a carrier oil film generally depends on the bearing load, the rotational speed, the working viscosity of the oil and the size of the bearing.
In the selection of oil, it is necessary to take the values found only by theoretical calculations (micro and macro geometries of the contact surfaces, lubrication at the time of rolling contact), but also to include experience values. Especially if the oil containing high pressure additives (EP additives) enters into a chemical reaction, this issue becomes even more important.
Greases are mineral or synthetic oils obtained by thickening with additives. Grease lubrication is the most common form of lubrication used in bearings. Greases, which minimize friction by forming a film layer between the rolling element and the ring raceways, vary widely according to the usage areas of the bearings (load, temperature, revolution, ambient conditions, etc.), this ratio is around 90% of all applications. It is necessary to analyze the conditions of use and to select the appropriate grease. Although the amount of grease to be put into the bearing varies according to the user's request, it is generally between 20%-30% of the internal volume of the bearing. These values may vary in special applications. For example, the amount of grease is reduced at high speeds. In general, the grease put into the bearing during manufacturing is sufficient for the entire operating life of the bearing.
Oil lubrication is generally applied when high speed or operating temperature is not suitable for grease use. In addition, oil lubrication is applied when low friction and heat removal from bearings, noise and vibration reduction are required. Oil bath, splash - impact lubrication, drip lubrication, circulation lubrication, mist and air-oil mixture lubrication, spray lubrication are various types of oil lubrication.
Packaging Materials
In general, packaging is made for protection against rust and the conservation oil or VCI used at this stage plays an important role. Packaging types (single boxed, single nylon, bulk, special design, etc.), materials used for packaging vary according to the demands of the customers and the way of transportation.
Accessories
In some bearings, components (parts) called accessories are needed due to application differences or design requirements. In this context, pressure sleeve, plastic sleeve, nut, felt, sheet metal casing, compression spring, etc. The design of the named products is also needed. At this stage, bearings are sold under the name of a set together with the appropriate accessories.